Tensile Fabrics knowledge (part 1)
18/02/2020 | Blog
Tensile fabric structures have existed for a very long time in the form of simple tent-like shelters; together, guy ropes and tent poles provide pre-tension to a fabric, allowing the greater structure to withstand the loads of wind, rain and snow.
Since the initial invention of tents, things have come a long way. With the rigorous work and analysis of architects like Frei Otto, who was “obsessed with tensile structures,” along with steady technological progress, it has become much easier to create all sorts of ingenious fabric geometries. In turn, large-scale tensile structures have increasing in both popularity and complexity over the past few decades.
Grounded in these advancements, today’s architects are harnessing tensile fabric structures in the form of sweeping roofs, dramatic canopies and dismountable and relocatable pavilions. As designers and architects experiment with the creative boundaries of these forms, tensile fabric structures continue to take on shocking curved, spiky and round profiles, as well as new and unthinkable combinations of these shapes.
While endless dramatic shapes are possible, many tensile fabrics structures are derivations of two shapes: the saddle and the cone. The saddle is a hyperbolic paraboloid, which means that the fabric surface is characterized by two high peaks and to low points; in other words, the saddle can be conceptualized as a warped rectangular grid. The cone resembles a volcano and is characterized by stacked radians or hoops.
According to J&J Carter, “These two forms can be combined to create an infinite number of permutations, much like the circle and the square with classical architecture.”
Two of the most common coated fabrics are Poly Vinyl Chloride (PVC) coated polyester and Poly Tetra Fluro Ethlene (PTFE) coated glass cloth.
Despite PVC’s durability and low-price, unlike many other polymers PVC contains chlorine, which has proven negative health effects on humans. Its chemical additives can also have a very negative effect on the recycling process of PVC materials. For this reason, architects such as Perkins+Will as well as leading material rating systems such as Cradle to Cradle and Living Building Challenge suggest that the only way to avoid the health hazards associated with PVC, is to eliminate it altogether.
One of the most remarkable qualities of PTFE is that it is actively bleached by UV light, which means that it is easy to maintain a crisp bright white appearance over the course of decades. This means that before installation, PTFE actually has an irregular off-white or slightly brown color, which results from the manufacturing and fabrication process. In addition, the coating resists the build up of environmental pollution and is naturally cleaned off by the rain.
PTFE coated glass cloth is available in various strength ranges. Typically, thicker fabrics will have a greater tensile strength and a lower light transmission rate, while lighter grade fabrics will have a lower tensile strength but greater daylighting and illumination effects.
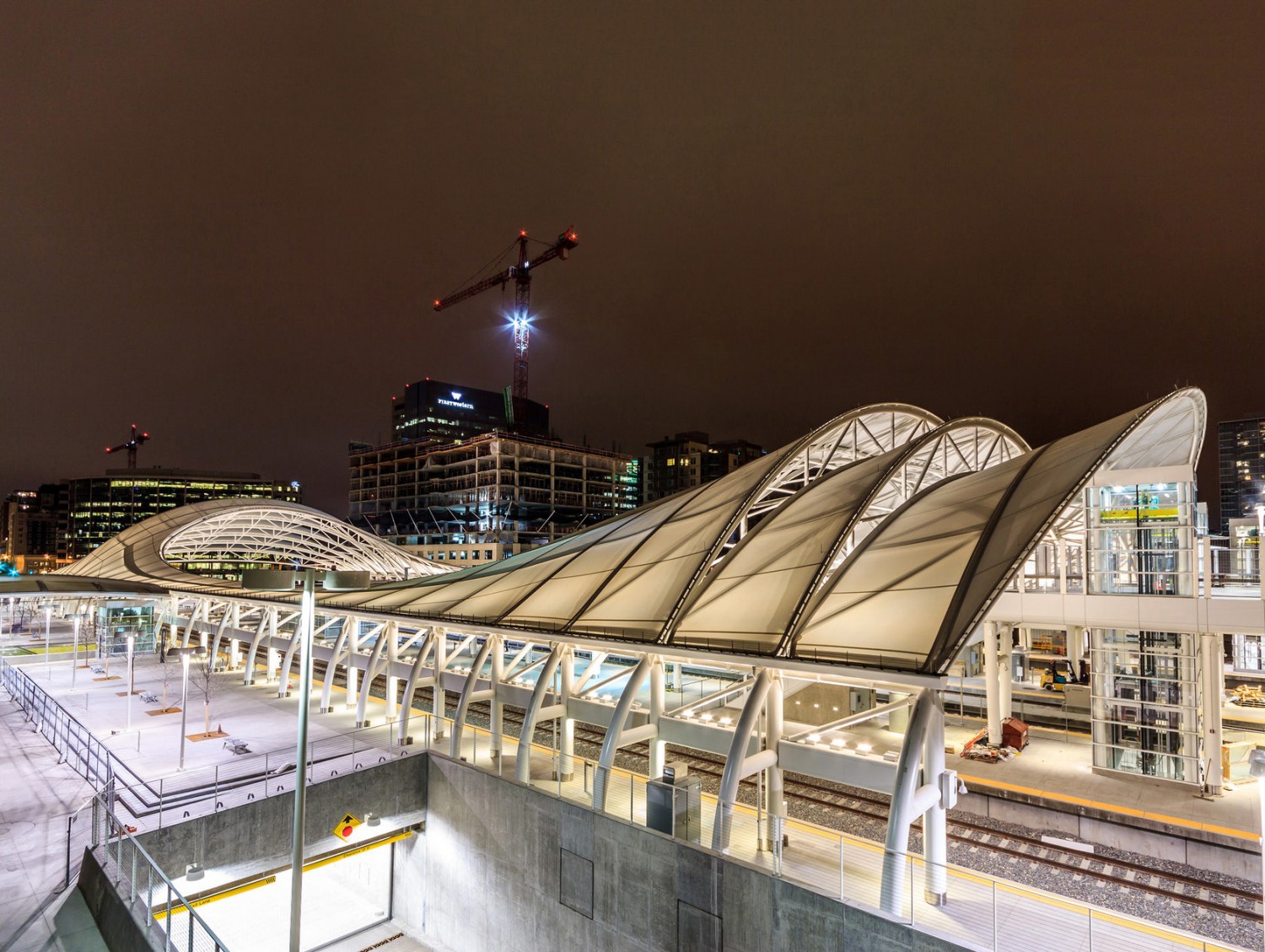
Grounded in these advancements, today’s architects are harnessing tensile fabric structures in the form of sweeping roofs, dramatic canopies and dismountable and relocatable pavilions. As designers and architects experiment with the creative boundaries of these forms, tensile fabric structures continue to take on shocking curved, spiky and round profiles, as well as new and unthinkable combinations of these shapes.
Tensile Fabric Systems
A tensile fabric structure is characterized by the tensioning of a fabric membrane system, using cables, wires, steel or any other form of support system. By tensioning the fabric, not only are creases eliminated, creating a clean appearance, but the material is also fortified to withstand weather conditions or potential damage.While endless dramatic shapes are possible, many tensile fabrics structures are derivations of two shapes: the saddle and the cone. The saddle is a hyperbolic paraboloid, which means that the fabric surface is characterized by two high peaks and to low points; in other words, the saddle can be conceptualized as a warped rectangular grid. The cone resembles a volcano and is characterized by stacked radians or hoops.
According to J&J Carter, “These two forms can be combined to create an infinite number of permutations, much like the circle and the square with classical architecture.”
Materials
Today’s innovative tensile fabrics can be broadly categorized into coated and mesh fabrics. Coated tensile fabrics are made with a woven cloth fabrics that are stabilized with a protective a coating in all directions. These fabrics are typically for external use, and are therefore the focus of this article’s exploration. While mesh fabrics are also a type of coated cloth, there are small spaces between the thread bundles and are thus more common among interior sun-shading applications.Two of the most common coated fabrics are Poly Vinyl Chloride (PVC) coated polyester and Poly Tetra Fluro Ethlene (PTFE) coated glass cloth.
PVC Coated Polyester:
PVC coated polyester can be a great material choice for both permanent and temporary tensile fabric structures. PVC coated polyester is known for its excellent strength, flexibility, translucency and affordability compared to PTFE coated glass cloth and ETFE. The PVC coating, which is applied to polyester includes UV stabilizers, fire retardant additives, and anti-fungicides. PVC coated polyester fabrics have a structural lifespan greater than 20 years. However, you may begin to experience some visual inconsistency earlier than 20 years because the surface grows harder to clean with time. For this reason, manufacturers may only quote a lifespan of 10-15 years.Despite PVC’s durability and low-price, unlike many other polymers PVC contains chlorine, which has proven negative health effects on humans. Its chemical additives can also have a very negative effect on the recycling process of PVC materials. For this reason, architects such as Perkins+Will as well as leading material rating systems such as Cradle to Cradle and Living Building Challenge suggest that the only way to avoid the health hazards associated with PVC, is to eliminate it altogether.
PTFE Coated Glass Cloth:
PTFE coated glass cloth was developed by DuPont in the 1960s and has been used to create tensile fabric structures since the early 1970s. Originally, the material had a lifespan of 25 years; however, this has already been exceeded, with present day expectations lying somewhere between 30 and 50 years. Today, it is considered to be the highest quality material for creating tensile fabric membranes and the best choice if you desire a long lifespan and low maintenance.One of the most remarkable qualities of PTFE is that it is actively bleached by UV light, which means that it is easy to maintain a crisp bright white appearance over the course of decades. This means that before installation, PTFE actually has an irregular off-white or slightly brown color, which results from the manufacturing and fabrication process. In addition, the coating resists the build up of environmental pollution and is naturally cleaned off by the rain.
PTFE coated glass cloth is available in various strength ranges. Typically, thicker fabrics will have a greater tensile strength and a lower light transmission rate, while lighter grade fabrics will have a lower tensile strength but greater daylighting and illumination effects.
ETFE:
While ETFE is a film rather than a fabric, it is worth touching on because it is commonly used as an alternative to structural glass and is rapidly growing in its applications. ETFE is an excellent choice if thermal insulation is a priority of your project. For a deeper exploration of ETFE building membranes, check out Architizer’s article: Glow Up: 8 Project Capturing the Power of ETFE Plastic.Source: Architizer